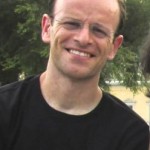
Figura professionale: Ingegnere
Nome Cognome | : E. C. | Età | : 47 |
---|---|---|---|
Cellulare/Telefono | : Riservato! | : Riservato! | |
CV Allegato | : Riservato! | Categoria CV | : Engineering |
Sede preferita | : Firenze |
Accesso Full al database con 30.001 CV a partire da € 5,00 ABBONATI SUBITO!
Sommario
Competenze
- HTML, NASTRAN/PATRAN, ANSYS, CATIA, MS OFFICE, Photoshop, Latex, Turbo Pascal, Fortran77s, Windows, Linux, Ubuntu, Unix
Lingue Parlate
- Francese,
- Inglese,
- Italiano,
- Spagnolo
Studi
Laurea Ingegneria Aerospaziale, Albo degli Ingegneri.
Esperienze
· FEM Analyst at Aernnova Aerospace (Vitoria-Gasteiz, Spain) – Self Employed
2016 (3 months)
A350-1000 FTE (Fixed Trailing Edge), Middle IFEM, Inner IFEM
• Migration of Pressure loads on structural panels using the Aerodynamic Original Mesh given as *.csv file as starting point.
• Modification and preprocessing of CFD Mesh grid in Patran
• Creation of Session files (*.ses) in Patran in order to pre-process a large amount of data
Gas Turbines Lead Engineer at GE Oil & Gas (Florence, Italy)
2011 – 2013 (2 years 7 months)
Gas turbine engineering dept.
Rotor Life Management (RLM) Technical Leader:
• Team leadership on analyses and risk assessments in support of RLM activities. Types of analysis include LCF, Creep and Crack Growth.
• Support on defining engineering processes, material testing, non-destructive inspections and rotor refurbishment advancements for RLM program.
• Define and develop life management policies updates and procedures
• Coordinate projects between different offices: operability, product service, repair engineering, product line, sales.
• Full responsibility on fulfilment activities to deliver rotor life extensions to Customers
· FEM Analyst at Alestis Aerospace S.L. (Getafe, Spain)
2008 – 2011 (2 years)
FEM analysis, Section 19.1 Airbus A350Xwb
• Linear GAPs technique implementation;
• Intact and FailSafe loadcases FE analysis.
Power Plant Integration FEM, Airbus Military A400M:
• FEM Nacelle Cowlings and Engine Mounting System interface;
Nacelle Cowlings, Airbus Military A400M:
• Dimensioning of Lower Structure Cowlings under Ultimate & Fail Safe Conditions.
· Research Engineer at CIRA (Capua, Italy)
2006 – 2007 (2 years)
Development of a progressive damage FEM analysis to design damage tolerant composite panels
· CAD Engineer at Aerosoft S.p.A. (Naples, Italy)
2005 (6 months)
CAD Modelling of composite primary fuselage structure Boeing 787, Fuselage Section 46.
Languages
Italian(Mother tongue)
English(Written and spoken, Fluent)
Spanish(Written and spoken, Fluent)
French (Beginner)
Education Università degli Studi di Napoli 'Federico II' – Italy
Master of Engineering in Aerospace Engineering, 1997 –2004
Grade: 110/110 cum Laude
Courses / Technical Training
As Gas Turbine Engineer (GE Oil & Gas)
– ISIGHT Fiper – GE (Florence, 2013)
As FEM Analyst (Alestis Aerospace)
– ISAMI Analyst Training -Airbus France Learning Services (Getafe, 2009)
– A350 Composite Fuselage Stress -EADS France Learning Services (Se villa, 2010)
As Research Engineer (CIRA)
– Aircraft Fatigue and Damage Tolerance –Cranfield University (UK, 2006)
– Composite Material Science -Univ. of Surrey (UK, 2006)
– ANSYS Workbench 11 -EnginSoft (Capua -Italy, 2007)
As CAD Engineer (Aerosoft)
– CATIA V5, ENOVIA LCA V5 – Boeing Company (Pomigliano d'Arco -Italy, 2005)
IT Tools: PATRAN, NASTRAN, ANSYS, ANSYS APDL, CATIA, MS Office, Aerodynamic Vortex Lattice Codes, Latex, Photoshop, Textpad, iSIGHT/Fiper 5.6, Fortran77, HTML, Pascal, Matlab, SolidWorks, AutoCad
Operative Systems: UNIX, Windows.
156 total views, 2 today